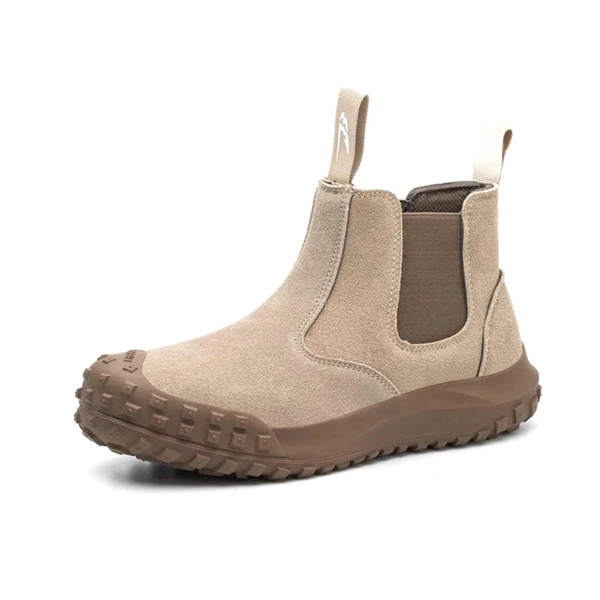
Burning Bright Through the Years: My Cowhide Boots’ Welding Legacy
It was the spark that nearly ended my career. July 2018, middle of a heatwave, and I was rushing to finish fabricating support beams for a commercial building renovation. One careless moment, one stray spark that found its way between my pant leg and boot, and suddenly I was doing the “hot foot dance” that every welder dreads. Three weeks of missed work and a nasty second-degree burn later, I made a decision that changed everything: no more compromising on foot protection.
27 Years in the Fire: A Welder’s Journey
The first thing my old man taught me when I started apprenticing in his shop at 16 was simple: “Your gear is your guardian.” But like most kids, I had to learn it the hard way. Now, after nearly three decades of standing in the line of fire—quite literally—I’ve learned that the right boots aren’t just another tool; they’re your foundation.
Those yellow waterproof welding boots with the Chelsea-style slip-on design caught my eye at a trade show in Milwaukee. The rep was doing demonstrations, pouring water over them, dropping weights on the steel toe, and even holding a torch near the cowhide upper to show how the sparks just bounced off. I was skeptical—we all are after enough years in the trade—but desperate enough to try something new.
The First Test: Baptism by Fire
My first real test came during a pipeline project in northern Minnesota. Twelve-hour shifts, temperatures dropping to -15°F, and working in conditions where removing your gloves for more than a minute risked frostbite. Most boots would crack or stiffen like cardboard, but these maintained flexibility I hadn’t experienced before.
“Hey Tom, what’s with the fancy yellow boots?” my foreman Dave joked during the morning briefing. By lunchtime, he was asking where to get a pair after watching me comfortably kneeling in slush while everyone else complained about wet socks.
But the real moment of truth came when I was cutting through a section of 2-inch steel pipe with an oxy-acetylene torch. A shower of molten metal rained down directly onto my right boot. I tensed, waiting for the pain… but nothing happened. The sparks scattered off the suede cowhide like water off a duck’s back. That night, I called my wife and told her, “I think I finally found them—the last pair of welding boots I’ll ever need to buy.”
What Makes Them Different: A Technical Breakdown
After four years and countless jobsites, I’ve put these boots through conditions that would have destroyed lesser footwear several times over. Here’s what I’ve learned about why they perform so well:
Feature | Official Specification | What It Means in Real Life |
---|---|---|
Steel Safety Toe | Meets EU and US safety standards (CE ISO 20345:2011) | Survived a 75lb I-beam rolling across my foot with nothing but a funny story to tell |
Kevlar Puncture Protection | “Bulletproof” Kevlar fabric in sole system | Stepped on a 3-inch nail at a demo site and didn’t realize it until I saw it stuck in my boot during lunch break |
Rubber Sole | Enhanced slip, oil and abrasion resistance | Haven’t slipped once on the oily concrete floors that used to have me skating like an NHL rookie |
Chelsea Boot Design | Elastic side panel for easy on/off | Can kick these off at the door without untying laces—my wife’s favorite feature after I tracked slag through the living room once |
Spark Resistant Cowhide | Seam-sealed suede cowhide | The sparks that once sent me to urgent care now bounce off harmlessly |
Beyond Protection: The Comfort Factor
Ask any tradesperson who’s on their feet 10+ hours a day, and they’ll tell you: comfort isn’t a luxury, it’s a necessity. What surprised me most about these boots wasn’t just their protection but how they felt at the end of a long shift.
Before these, I had a post-work ritual that involved ibuprofen and soaking my feet. The lightweight design (about 30% lighter than my previous steel-toes) combined with the flexibility of that Kevlar midsole changed everything. My old boots felt like anchors; these move with my feet.
“You’re not walking like an old man anymore,” my apprentice Jake noted after a particularly grueling 14-hour day installing structural supports. He wasn’t wrong—I’m pushing 50 now, and these boots have me feeling 35 again.
The Test of Time: Four Years Later
The real test of any work gear isn’t how it performs when new—it’s how it holds up over time. After four years of daily abuse, here’s the honest assessment:
- The yellow leather has darkened slightly and developed character marks (or “patina” as my wife calls it to make me feel better about scuffed boots)
- The elastic side panels haven’t stretched out or lost their shape
- The steel toe remains firmly in place with no separation from the upper
- The rubber sole shows wear but still provides reliable traction
- The suede cowhide still repels sparks effectively
- They still keep my feet dry in wet conditions
Compare that to my previous boots that would be falling apart after 8-12 months, and the value proposition becomes clear. Yes, they cost more upfront, but I’ve saved money in the long run.
Beyond Welding: Versatility in the Field
While these boots excel in welding environments, their versatility has impressed me across different aspects of the job:
Electrical Work
Working near live circuits is part of the job sometimes. The electrical resistance of the rubber soles has given me peace of mind during those inevitable moments when you’re checking connections and there’s no time to change footwear.
During a manufacturing plant installation, I was helping the electricians pull cable when water from an overhead pipe unexpectedly sprayed across the area. Everyone scattered except me and an old-timer named Frank who was wearing similar boots. “Rubber soles,” he nodded at me with the knowing look of someone who’s survived enough jobsites to appreciate proper gear.
All-Weather Performance
I’ve worn these boots in Minnesota winters, Florida summer humidity, and everything in between. The waterproofing has kept my feet dry during surprise downpours, while the breathability has prevented that swampy feeling during hot days in the shop.
Mobility and Support
The 6-inch upper hits that sweet spot between ankle protection and mobility. I’ve scrambled up scaffolding, balanced on steel beams, and crouched in awkward positions to reach difficult welds—all without feeling restricted or unstable.
A Day in the Life: What These Boots Handle
To really understand what these boots endure, let me walk you through a typical day on a recent commercial construction project:
5:30 AM: Boots go on easily thanks to the Chelsea design—no fumbling with laces in the dark 6:00 AM: Job site walk-through in morning dew—feet stay dry 8:30 AM: Cutting steel beams with plasma cutter—sparks everywhere, boots unaffected 10:15 AM: Accidentally step in a puddle of cutting oil—no slipping, no seepage 12:30 PM: Quick boot removal for lunch break without the typical wrestling match 1:15 PM: Back to welding in a cramped corner, kneeling on concrete for two hours—feet uncomfortable (they’re not miracle workers) but not painful 3:45 PM: Helper drops a small pipe fitting on my foot—barely felt it 5:30 PM: End of day boot removal reveals dry socks and feet that aren’t screaming for relief
That’s the real test—not lab conditions or marketing claims, but the day-in, day-out punishment of actual work.
What My Crew Says: Testimonials from the Trenches
I’m not the only convert. After seeing my boots in action, five of my colleagues have made the switch. Their unfiltered feedback:
“First boots I’ve had where I don’t count the minutes until I can take them off.” – Ray, 20-year pipe fitter
“Thought the yellow would look ridiculous, but they’ve saved my toes twice now. They could be hot pink for all I care.” – Samantha, structural welder
“Best money I’ve spent on gear in 15 years. Period.” – Marcus, shop foreman
FAQ: What Every Welder Wants to Know
How long is the break-in period?
About 3-4 days of regular wear. The cowhide softens quickly, but without compromising protection. Pro tip: wear them around the house with thick socks for a day before taking them to work.
How do they handle extreme heat?
I’ve tested these with ambient temperatures up to 110°F in a metal fabrication shop with poor ventilation. While no boot is comfortable in those conditions, these breathe better than most safety boots I’ve worn. The spark protection has never failed, even when working directly with 5000°F+ welding arcs.
Are they truly waterproof or just water-resistant?
In my experience, truly waterproof. I’ve stood in ankle-deep water for over an hour during an emergency repair job, and my socks stayed completely dry. After four years, they still keep water out effectively.
How do they compare to lace-up welding boots?
The Chelsea design initially concerned me—I was worried about ankle support and security. In practice, they provide comparable support to laced boots when properly sized. The convenience factor of slip-on design is significant, especially when moving between indoor and outdoor environments.
What’s the best way to care for the cowhide to maintain spark resistance?
Clean regularly with a suede brush to remove embedded metal particles. Avoid petroleum-based conditioners which can compromise fire resistance. I use a silicone-free suede protector spray twice a year, and that’s it.
The Investment Perspective: Why Quality Pays Off
Let’s talk numbers. These boots cost me approximately $60 more than the mid-range safety boots I used to buy. However:
- They’ve lasted 4+ years versus my previous boots’ average of 10 months
- I haven’t missed a single day of work due to foot injuries (my previous average was 3-4 days per year)
- I no longer buy specialized insoles to compensate for inadequate comfort
- My physiotherapist noted improved posture and reduced back strain
With journeyman welders in my area making $32-38/hour, even a single day of missed work more than covers the additional cost. Factor in the extended lifespan, and these boots aren’t an expense—they’re an investment with measurable returns.
The Bottom Line: A Welder’s Essential
After nearly three decades in trades where my feet are constantly threatened by heavy objects, sharp debris, molten metal, and harsh conditions, I’ve learned that compromise isn’t an option. These waterproof Chelsea-style welding boots with their steel toe protection, Kevlar puncture resistance, and spark-resistant cowhide have fundamentally changed my relationship with work.
They’ve been with me through pipeline projects in Minnesota, structural work in Florida, and countless fabrication jobs in my home shop. They’ve protected me from injuries that would have sent me home or to the hospital, kept me comfortable during 14-hour shifts, and saved me money in the long run.
If you spend your days with your feet planted firmly in the line of fire—whether you’re welding, cutting, grinding, or building—do yourself a favor. Don’t wait for the spark that sends you home. Invest in proper protection now, and feel the difference that quality makes when you’re still standing comfortable and injury-free at the end of a long day. 🔥👢
Ready to experience the difference that professional-grade foot protection can make? Check out these Waterproof Welding Safety Boots and join the thousands of tradespeople who’ve upgraded their safety and comfort on the job.
About the author: Thomas Weldman is a certified AWS (American Welding Society) instructor with 27 years of field experience spanning structural, pipeline, and fabrication welding. He currently runs a custom metal fabrication shop and conducts safety training seminars for apprentice welders across the Midwest.