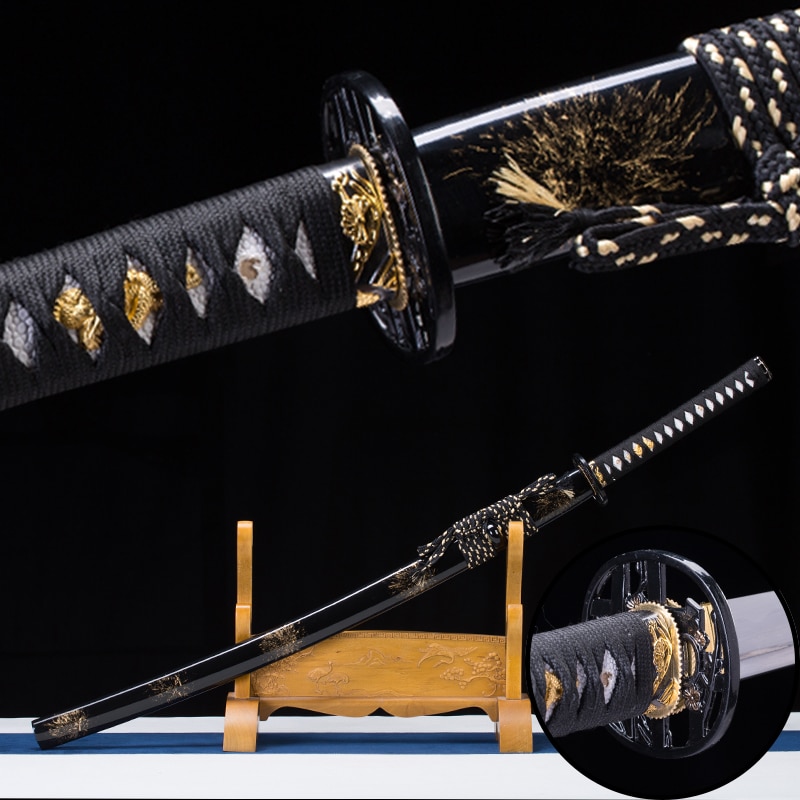
The art of crafting a Katana, the iconic Japanese sword, is steeped in centuries of tradition and meticulous craftsmanship. Over the years, however, modern techniques have emerged to complement or even challenge the time-honored methods. This article explores the differences between traditional Katana forging and modern manufacturing processes, providing insights into the artistry, efficiency, and quality of both approaches.
Traditional Katana Forging: An Art Passed Down Through Generations
Traditional Katana forging is a labor-intensive and spiritually significant process that involves several key steps. Each stage reflects centuries of Japanese craftsmanship and cultural reverence.
1. Materials and the Role of Tamahagane
Traditional Katanas are crafted using Tamahagane, a high-carbon steel made from iron sand. This material is smelted in a tatara furnace, an ancient Japanese technique requiring constant monitoring to achieve the correct steel composition.
- Advantage: Tamahagane offers the perfect balance of strength and flexibility, making it ideal for swords that must endure rigorous use.
- Challenge: The process is time-consuming and resource-intensive, with only small quantities of Tamahagane produced in each smelting cycle.
2. Folding and Forging
The hallmark of a traditional Katana is its folded steel blade. Swordsmiths fold the steel multiple times to remove impurities and create a unique grain pattern (hada).
- Advantage: This technique aligns the carbon content, ensuring a blade that is strong yet pliable.
- Challenge: Folding requires immense skill to avoid weakening the steel or introducing structural flaws.
3. Differential Hardening and Hamon
Traditional forging includes differential hardening, where the blade’s edge is coated with clay and heated, followed by rapid cooling. This creates a hardened edge and a softer spine, resulting in a durable blade with a visible temper line (hamon).
- Advantage: The process ensures a razor-sharp edge while maintaining flexibility to absorb shocks.
- Challenge: Achieving a flawless hamon demands precision, and any misstep can ruin the blade.
4. Time and Craftsmanship
Each traditionally forged Katana can take weeks or even months to complete. Every step is performed by hand, requiring expertise passed down through generations.
Modern Katana Forging Techniques: Balancing Efficiency and Innovation
Modern methods of forging Katanas have been developed to streamline production, meet demand, and reduce costs while retaining essential qualities of the sword.
1. Use of Modern Steels
Instead of Tamahagane, modern Katanas often use high-quality industrial steels like 1095 carbon steel, Damascus steel, or stainless steel. These materials offer consistency and are easier to source.
- Advantage: Modern steels provide comparable durability and sharpness without the exhaustive smelting process.
- Challenge: They lack the historical and cultural authenticity of Tamahagane.
2. Machine-Assisted Forging
Modern production incorporates machinery for processes like shaping, grinding, and polishing. While not eliminating human involvement, it significantly reduces labor time.
- Advantage: Machines ensure uniformity, especially for mass-produced Katanas.
- Challenge: Automated techniques cannot replicate the unique characteristics of hand-forged blades.
3. Chemical Hardening and Coating
Differential hardening is sometimes replaced by chemical treatments or heat tempering processes to achieve a hardened edge and flexible spine.
- Advantage: These methods are faster and reduce the risk of error during hardening.
- Challenge: They lack the artistry and visual appeal of a traditional hamon.
4. Mass Production and Affordability
Modern techniques enable the production of functional Katanas at a fraction of the cost of traditional blades.
- Advantage: Affordable options allow enthusiasts to own Katanas without breaking the bank.
- Challenge: Mass production may sacrifice uniqueness, historical value, and the intricate craftsmanship of traditional forging.
Key Differences Between Traditional and Modern Methods
Aspect | Traditional Forging | Modern Techniques |
---|---|---|
Materials | Tamahagane | Industrial steels (e.g., 1095, Damascus) |
Process | Hand-forged and folded | Machine-assisted |
Hardening | Differential hardening with clay | Chemical or heat treatment |
Production Time | Weeks to months | Days to weeks |
Cost | High | Affordable |
Uniqueness | Each blade is unique | Uniform designs |
Which Is Better? It Depends on Your Purpose
For Collectors and Purists
If authenticity, tradition, and artistry are paramount, a traditionally forged Katana is unparalleled. These blades carry cultural and historical significance, making them ideal for collectors and martial artists who value heritage.
For Practical Users and Budget-Conscious Buyers
Modern Katanas offer excellent functionality and affordability, making them suitable for beginners, reenactors, and casual enthusiasts. They provide durability and performance without the steep price tag of traditional blades.
Conclusion
The choice between a traditional and modern Katana ultimately depends on your priorities. Traditional methods celebrate centuries of craftsmanship, resulting in one-of-a-kind masterpieces, while modern techniques provide accessibility and practicality for a broader audience.
Whether you’re a collector seeking an heirloom-quality blade or an enthusiast looking for a reliable sword, understanding these differences ensures you’ll find the perfect Katana for your needs.